Destylatory przemysłowe znajdują szerokie zastosowanie w wielu branżach, co sprawia, że są niezbędnym elementem nowoczesnej produkcji. W przemyśle chemicznym destylatory służą do separacji składników mieszanin ciekłych, co pozwala na uzyskanie czystych substancji chemicznych. W branży petrochemicznej wykorzystuje się je do rafinacji ropy naftowej, gdzie różne frakcje są oddzielane w procesie destylacji frakcyjnej. W przemyśle spożywczym destylatory odgrywają kluczową rolę w produkcji alkoholi, takich jak wódka czy whisky, gdzie proces destylacji pozwala na uzyskanie odpowiedniej mocy i smaku trunku. Ponadto, w przemyśle farmaceutycznym destylacja jest wykorzystywana do oczyszczania substancji czynnych oraz rozpuszczalników.
Jakie są kluczowe elementy budowy destylatora przemysłowego
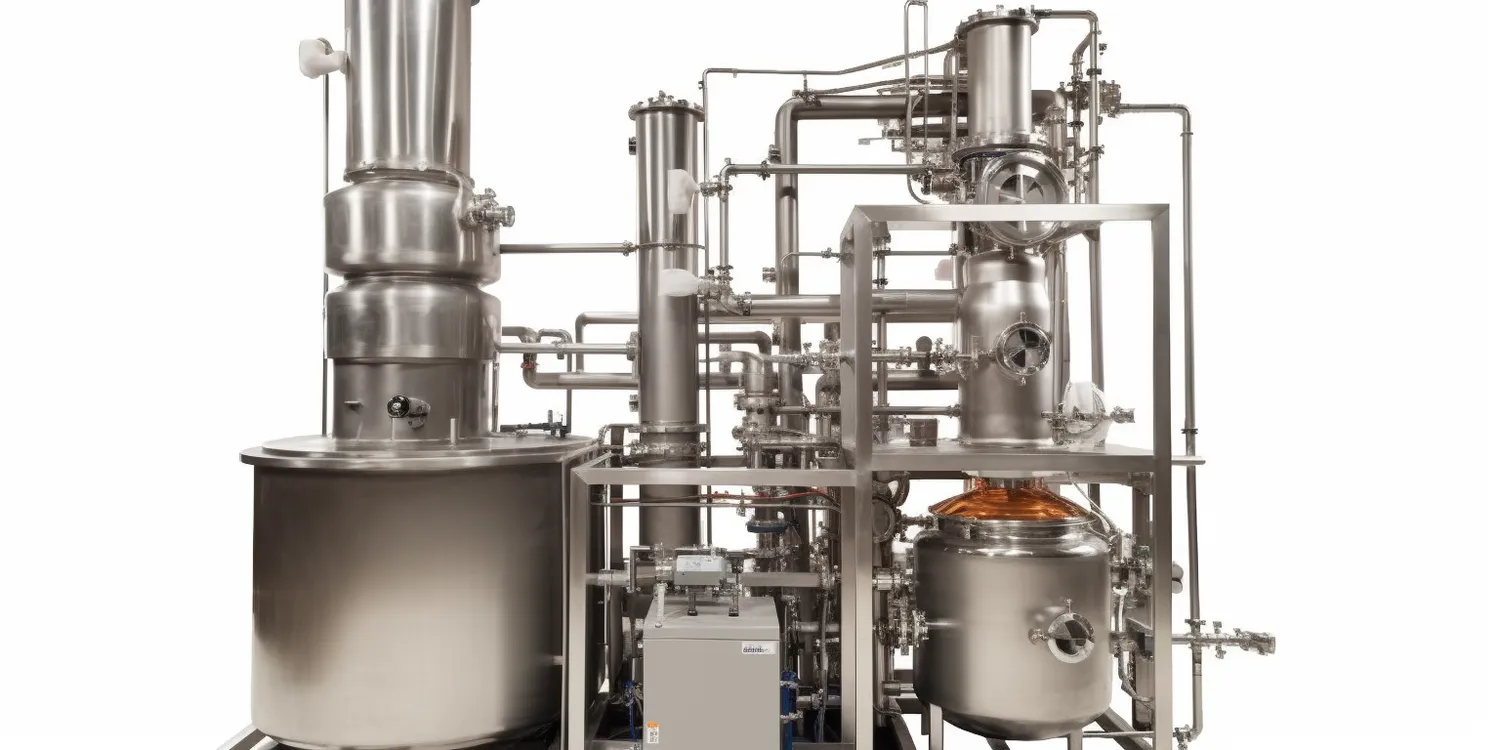
Budowa destylatora przemysłowego opiera się na kilku kluczowych elementach, które współpracują ze sobą, aby zapewnić efektywny proces destylacji. Podstawowym komponentem jest zbiornik, w którym umieszczana jest mieszanina cieczy do destylacji. Zbiornik ten często wyposażony jest w system grzewczy, który podgrzewa ciecz do odpowiedniej temperatury, umożliwiając jej parowanie. Kolejnym istotnym elementem jest kolumna destylacyjna, która ma za zadanie separację pary od cieczy. W kolumnie tej znajdują się różnego rodzaju elementy, takie jak złoża czy talerze, które zwiększają powierzchnię kontaktu między parą a cieczą, co prowadzi do lepszej separacji składników. Po przejściu przez kolumnę para trafia do skraplacza, gdzie schładza się i kondensuje z powrotem do postaci cieczy. Ostatnim kluczowym elementem jest system odbioru produktu końcowego, który pozwala na zbieranie oczyszczonego płynu.
Jakie są najważniejsze zalety używania destylatorów przemysłowych
Używanie destylatorów przemysłowych niesie ze sobą wiele korzyści, które mają znaczący wpływ na efektywność procesów produkcyjnych oraz jakość finalnych produktów. Przede wszystkim destylacja pozwala na uzyskanie wysokiej czystości substancji chemicznych, co jest kluczowe w wielu branżach, takich jak farmaceutyka czy chemia przemysłowa. Dzięki precyzyjnemu procesowi separacji możliwe jest oddzielenie pożądanych składników od zanieczyszczeń czy niepożądanych substancji. Kolejną zaletą jest możliwość skalowania procesu – destylatory przemysłowe mogą być dostosowane do różnych wielkości produkcji, co pozwala firmom na elastyczne reagowanie na zmieniające się potrzeby rynku. Dodatkowo nowoczesne destylatory są często wyposażone w zaawansowane systemy automatyzacji i monitoringu, co zwiększa efektywność operacyjną oraz redukuje ryzyko błędów ludzkich.
Jakie są najnowsze technologie stosowane w destylatorach przemysłowych
W ostatnich latach rozwój technologii związanych z destylacją przyniósł wiele innowacji, które znacząco poprawiły wydajność i efektywność działania destylatorów przemysłowych. Jedną z najważniejszych nowości jest zastosowanie technologii membranowej, która umożliwia separację składników bez konieczności podgrzewania cieczy. To podejście nie tylko zmniejsza zużycie energii, ale także minimalizuje ryzyko degradacji termicznej cennych substancji. Innym interesującym rozwiązaniem są systemy hybrydowe łączące tradycyjne metody destylacji z nowoczesnymi technologiami ekstrakcji czy adsorpcji. Takie podejście pozwala na jeszcze skuteczniejsze oddzielanie składników o podobnych właściwościach fizykochemicznych. Dodatkowo coraz częściej stosuje się inteligentne systemy monitorowania i zarządzania procesem destylacji, które wykorzystują sztuczną inteligencję i analizę danych do optymalizacji parametrów pracy urządzenia w czasie rzeczywistym.
Jakie są kluczowe czynniki wpływające na wydajność destylatorów przemysłowych
Wydajność destylatorów przemysłowych jest determinowana przez szereg czynników, które mają istotny wpływ na efektywność całego procesu destylacji. Jednym z najważniejszych elementów jest temperatura, która musi być odpowiednio dobrana do rodzaju substancji poddawanej destylacji. Zbyt niska temperatura może prowadzić do niepełnej separacji składników, natomiast zbyt wysoka może powodować ich degradację. Kolejnym kluczowym czynnikiem jest ciśnienie, które również wpływa na punkt wrzenia cieczy i tym samym na efektywność procesu. W wielu nowoczesnych destylatorach stosuje się systemy umożliwiające regulację ciśnienia, co pozwala na optymalizację warunków pracy w zależności od specyfiki przetwarzanej mieszaniny. Ważnym aspektem jest także konstrukcja kolumny destylacyjnej, której wysokość oraz rodzaj zastosowanych elementów separacyjnych mają bezpośredni wpływ na jakość i ilość uzyskanego produktu.
Jakie są różnice między destylacją prostą a frakcyjną w kontekście przemysłowym
Destylacja prosta i frakcyjna to dwa podstawowe procesy wykorzystywane w przemyśle do separacji składników mieszanin ciekłych, jednak różnią się one zasadniczo pod względem zastosowania oraz efektywności. Destylacja prosta polega na jednorazowym podgrzaniu cieczy do momentu jej wrzenia i skropleniu pary, co sprawia, że jest to metoda stosunkowo prosta i szybka. Jest ona najczęściej wykorzystywana w przypadku substancji o znacznie różniących się temperaturach wrzenia lub w sytuacjach, gdy wymagana jest niewielka ilość produktu. Z kolei destylacja frakcyjna to bardziej zaawansowany proces, który wykorzystuje kolumnę destylacyjną z wieloma poziomami separacyjnymi. Dzięki temu możliwe jest oddzielanie składników o zbliżonych temperaturach wrzenia poprzez wielokrotne parowanie i skraplanie, co prowadzi do uzyskania wyższej czystości produktów końcowych.
Jakie są koszty eksploatacji destylatorów przemysłowych
Koszty eksploatacji destylatorów przemysłowych mogą być znaczące i obejmują różnorodne aspekty związane z ich użytkowaniem. Przede wszystkim należy uwzględnić koszty energii potrzebnej do podgrzewania cieczy w procesie destylacji. W zależności od zastosowanej technologii oraz źródła energii, te wydatki mogą stanowić dużą część całkowitych kosztów operacyjnych. Dodatkowo ważnym elementem są koszty związane z konserwacją i serwisowaniem urządzeń, które są niezbędne dla zapewnienia ich prawidłowego działania oraz długowieczności. Regularne przeglądy techniczne oraz wymiana zużytych części mogą generować dodatkowe wydatki, które należy uwzględnić w budżecie przedsiębiorstwa. Nie można także zapominać o kosztach materiałów eksploatacyjnych, takich jak chemikalia używane do czyszczenia czy dodatki wspomagające procesy separacyjne. Warto również zwrócić uwagę na koszty związane z przestrzeganiem norm środowiskowych oraz bezpieczeństwa pracy, które mogą wiązać się z koniecznością inwestycji w dodatkowe systemy filtracyjne czy zabezpieczające.
Jakie są najczęstsze problemy występujące w pracy destylatorów przemysłowych
Praca destylatorów przemysłowych może wiązać się z różnorodnymi problemami technicznymi, które mogą wpłynąć na efektywność procesu oraz jakość uzyskiwanego produktu. Jednym z najczęstszych problemów jest tzw. “fouling”, czyli osadzanie się zanieczyszczeń na powierzchniach wymiany ciepła w kolumnach czy skraplaczach. To zjawisko prowadzi do obniżenia efektywności wymiany ciepła oraz zwiększa zużycie energii. Innym powszechnym problemem jest niestabilność procesu spowodowana zmianami temperatury lub ciśnienia, co może prowadzić do niepełnej separacji składników i obniżenia jakości produktu końcowego. W przypadku destylacji frakcyjnej mogą wystąpić także trudności związane z nadmiernym obciążeniem kolumny, co skutkuje spadkiem wydajności i koniecznością przeprowadzenia dodatkowych regulacji. Problemy mogą także wynikać z niewłaściwego doboru materiałów konstrukcyjnych lub uszczelek, co prowadzi do wycieków substancji chemicznych i zagrożeń dla zdrowia pracowników oraz środowiska.
Jakie są przyszłe kierunki rozwoju technologii destylacyjnych
Przyszłość technologii destylacyjnych zapowiada się bardzo obiecująco dzięki ciągłemu postępowi naukowemu oraz innowacjom technologicznym. Wśród najważniejszych kierunków rozwoju można zauważyć rosnącą tendencję do automatyzacji procesów produkcyjnych, co pozwala na zwiększenie efektywności operacyjnej oraz redukcję błędów ludzkich. Systemy oparte na sztucznej inteligencji będą coraz częściej wykorzystywane do monitorowania parametrów pracy urządzeń oraz optymalizacji procesów w czasie rzeczywistym. Kolejnym istotnym trendem jest rozwój technologii zielonej chemii, która stawia nacisk na minimalizację negatywnego wpływu procesów przemysłowych na środowisko naturalne. W tym kontekście poszukiwane są nowe metody separacji składników bez użycia dużych ilości energii czy toksycznych rozpuszczalników. Dodatkowo badania nad nowymi materiałami konstrukcyjnymi dla kolumn i skraplaczy mogą przyczynić się do poprawy efektywności energetycznej urządzeń oraz zwiększenia ich trwałości.
Jakie są kluczowe aspekty bezpieczeństwa w pracy destylatorów przemysłowych
Bezpieczeństwo w pracy destylatorów przemysłowych jest niezwykle istotnym zagadnieniem, które wymaga szczególnej uwagi ze strony przedsiębiorstw. Przede wszystkim należy zapewnić odpowiednie szkolenie pracowników, aby byli świadomi potencjalnych zagrożeń związanych z obsługą urządzeń oraz umieli reagować w sytuacjach awaryjnych. Kluczowym elementem jest także stosowanie odpowiednich środków ochrony osobistej, takich jak odzież ochronna, rękawice czy gogle. Ważne jest również regularne przeprowadzanie inspekcji technicznych oraz konserwacji urządzeń, co pozwala na wczesne wykrywanie ewentualnych usterek i zapobieganie awariom. Dodatkowo, systemy monitorowania parametrów pracy destylatorów powinny być wyposażone w alarmy, które informują o nieprawidłowościach, takich jak nadmierne ciśnienie czy temperatura. W kontekście bezpieczeństwa istotne jest także przestrzeganie przepisów dotyczących składowania i transportu substancji chemicznych, aby zminimalizować ryzyko wycieków czy pożarów.