Destylacja rozpuszczalników to proces, który pozwala na oddzielenie różnych substancji chemicznych na podstawie ich temperatury wrzenia. Jest to jedna z najstarszych i najczęściej stosowanych metod separacji, wykorzystywana w laboratoriach oraz w przemyśle chemicznym. Proces ten polega na podgrzewaniu mieszaniny, co prowadzi do odparowania substancji o niższej temperaturze wrzenia. Następnie para jest schładzana, co powoduje jej kondensację i zbieranie w osobnym naczyniu. W ten sposób można uzyskać czysty rozpuszczalnik oraz inne składniki, które były obecne w pierwotnej mieszaninie. Destylacja rozpuszczalników jest szczególnie przydatna w przypadku cieczy, które mają różne właściwości fizyczne. Dzięki temu procesowi można uzyskać wysokiej jakości produkty chemiczne, które są niezbędne w wielu dziedzinach, takich jak farmacja, petrochemia czy produkcja żywności.
Jakie są zastosowania destylacji rozpuszczalników w przemyśle
Destylacja rozpuszczalników znajduje szerokie zastosowanie w różnych gałęziach przemysłu. W przemyśle chemicznym jest kluczowym procesem przy produkcji wielu substancji chemicznych, takich jak alkohole, kwasy organiczne czy estry. Dzięki destylacji możliwe jest uzyskanie wysokiej czystości produktów, co jest niezwykle istotne w kontekście ich dalszego wykorzystania. W branży farmaceutycznej destylacja odgrywa ważną rolę w produkcji leków oraz substancji czynnych. Czystość tych produktów jest kluczowa dla ich skuteczności oraz bezpieczeństwa stosowania. Ponadto destylacja rozpuszczalników znajduje zastosowanie w przemyśle spożywczym, gdzie wykorzystywana jest do produkcji aromatów oraz ekstraktów z roślin. W przemyśle petrochemicznym proces ten jest niezbędny do separacji różnych frakcji ropy naftowej, co pozwala na uzyskanie paliw oraz innych produktów naftowych.
Jakie są różnice między destylacją prostą a frakcyjną
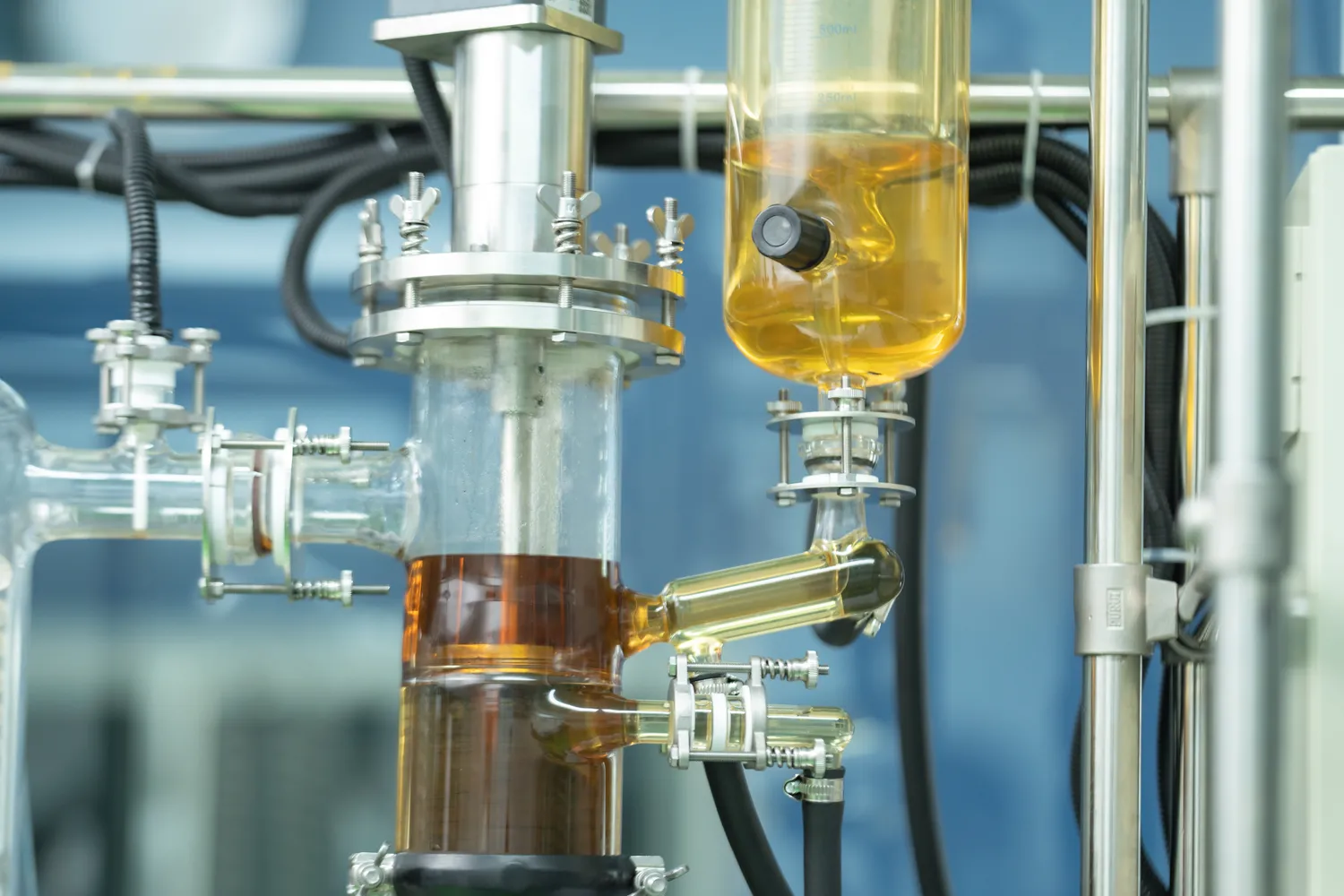
Destylacja prosta i frakcyjna to dwa podstawowe rodzaje procesów destylacyjnych, które różnią się pod względem zastosowania oraz efektywności separacji składników mieszaniny. Destylacja prosta jest najprostszą formą tego procesu i stosowana jest głównie do oddzielania substancji o znacznie różniących się temperaturach wrzenia. Proces ten polega na podgrzewaniu cieczy i zbieraniu pary, która następnie skrapla się w chłodnicy. Z kolei destylacja frakcyjna jest bardziej skomplikowaną metodą, która umożliwia oddzielanie składników o zbliżonych temperaturach wrzenia. W tym przypadku stosuje się kolumny frakcyjne, które zwiększają powierzchnię kontaktu pary z cieczą, co pozwala na wielokrotne skraplanie i odparowywanie składników. Dzięki temu możliwe jest uzyskanie wyższej czystości produktów końcowych. Destylacja frakcyjna jest szczególnie przydatna w przemyśle petrochemicznym oraz chemicznym, gdzie często zachodzi potrzeba separacji wielu składników o podobnych właściwościach fizycznych.
Jakie są zalety i ograniczenia destylacji rozpuszczalników
Destylacja rozpuszczalników ma wiele zalet, które sprawiają, że jest to popularna metoda separacji w różnych dziedzinach przemysłu i nauki. Jedną z głównych zalet tego procesu jest jego efektywność w uzyskiwaniu wysokiej czystości produktów końcowych. Dzięki możliwości precyzyjnego kontrolowania temperatury wrzenia można skutecznie oddzielać składniki o różnych właściwościach fizycznych. Kolejną zaletą jest wszechstronność tej metody – może być stosowana do różnych typów mieszanin oraz do szerokiego zakresu substancji chemicznych. Jednakże destylacja ma także swoje ograniczenia. Przede wszystkim nie zawsze jest możliwe oddzielenie składników o zbliżonych temperaturach wrzenia bez użycia dodatkowych technik, takich jak destylacja frakcyjna czy azeotropowa. Ponadto proces ten może być czasochłonny i wymaga znacznych nakładów energii do podgrzewania cieczy oraz chłodzenia pary.
Jakie są najczęstsze błędy podczas destylacji rozpuszczalników
Podczas przeprowadzania procesu destylacji rozpuszczalników, istnieje wiele pułapek, w które można wpaść, co może prowadzić do nieefektywności lub nawet uszkodzenia sprzętu. Jednym z najczęstszych błędów jest niewłaściwe ustawienie temperatury. Zbyt wysoka temperatura może prowadzić do niekontrolowanego odparowania substancji, co skutkuje stratą cennych składników oraz zanieczyszczeniem produktu końcowego. Z kolei zbyt niska temperatura może uniemożliwić efektywne oddzielenie składników, co również wpływa na jakość uzyskanego rozpuszczalnika. Kolejnym problemem jest niewłaściwe dobranie sprzętu destylacyjnego. Użycie kolumny frakcyjnej o niewłaściwej wysokości lub średnicy może znacznie obniżyć efektywność separacji. Ważne jest także, aby dokładnie monitorować proces i reagować na zmiany w temperaturze oraz ciśnieniu, które mogą wskazywać na problemy z destylacją. Inny błąd to niedostateczne oczyszczenie sprzętu przed rozpoczęciem procesu, co może prowadzić do kontaminacji i wpływać na wyniki analizy chemicznej.
Jakie są różne metody destylacji rozpuszczalników
Destylacja rozpuszczalników obejmuje różne metody, które są dostosowane do specyfiki separowanej mieszaniny oraz pożądanej czystości produktów końcowych. Oprócz destylacji prostej i frakcyjnej, istnieją także inne techniki, takie jak destylacja azeotropowa i destylacja próżniowa. Destylacja azeotropowa jest stosowana w przypadku mieszanin, które tworzą azeotropy, czyli mieszaniny o stałym składzie, które mają tę samą temperaturę wrzenia co ich składniki. W takim przypadku zwykle dodaje się substancję pomocniczą, która umożliwia oddzielenie składników poprzez zmianę ich właściwości fizycznych. Destylacja próżniowa z kolei polega na obniżeniu ciśnienia atmosferycznego w układzie destylacyjnym, co pozwala na obniżenie temperatury wrzenia substancji i minimalizację degradacji termicznej wrażliwych związków chemicznych. Inną metodą jest destylacja membranowa, która wykorzystuje membrany do separacji składników na podstawie ich wielkości cząsteczkowej lub właściwości chemicznych.
Jakie są kluczowe czynniki wpływające na efektywność destylacji
Efektywność destylacji rozpuszczalników zależy od wielu czynników, które mogą znacząco wpłynąć na jakość i ilość uzyskiwanych produktów. Jednym z kluczowych elementów jest temperatura wrzenia poszczególnych składników mieszanki. Różnice w temperaturach wrzenia pozwalają na skuteczne oddzielanie substancji; im większa różnica, tym łatwiejszy proces separacji. Kolejnym istotnym czynnikiem jest ciśnienie atmosferyczne, które wpływa na temperaturę wrzenia cieczy. W warunkach obniżonego ciśnienia można uzyskać lepsze wyniki przy separacji wrażliwych substancji chemicznych. Dodatkowo ważna jest konstrukcja sprzętu destylacyjnego; odpowiednio zaprojektowane kolumny frakcyjne czy chłodnice mogą znacznie zwiększyć efektywność procesu. Czas trwania destylacji również ma znaczenie; zbyt krótki czas może prowadzić do niepełnej separacji składników, podczas gdy zbyt długi czas może powodować straty materiałowe oraz degradację produktów.
Jakie są nowoczesne technologie związane z destylacją rozpuszczalników
W ostatnich latach rozwój technologii związanych z destylacją rozpuszczalników przyniósł wiele innowacyjnych rozwiązań, które zwiększają efektywność oraz bezpieczeństwo tego procesu. Jednym z takich rozwiązań są systemy automatyzacji procesów destylacyjnych, które umożliwiają precyzyjne monitorowanie i kontrolowanie parametrów operacyjnych w czasie rzeczywistym. Dzięki zastosowaniu czujników i oprogramowania komputerowego możliwe jest optymalizowanie warunków pracy urządzeń oraz minimalizowanie ryzyka błędów ludzkich. Innowacyjne technologie obejmują także zastosowanie nanomateriałów w konstrukcji kolumn frakcyjnych, co pozwala na zwiększenie powierzchni kontaktu pary z cieczą oraz poprawę efektywności separacji. Wprowadzenie technologii membranowych również przyczyniło się do rozwoju nowoczesnych metod separacyjnych; membrany umożliwiają selektywną filtrację składników mieszanki bez konieczności podgrzewania ich do wysokich temperatur.
Jakie są perspektywy rozwoju technologii destylacji rozpuszczalników
Perspektywy rozwoju technologii związanych z destylacją rozpuszczalników są obiecujące i wskazują na dalszy postęp w tej dziedzinie. W miarę jak rośnie zapotrzebowanie na czyste substancje chemiczne oraz ekologiczne metody produkcji, techniki separacyjne będą musiały ewoluować i dostosowywać się do nowych wymagań rynkowych. Przykładem mogą być innowacje związane z biotechnologią; wykorzystanie enzymów czy mikroorganizmów do separacji składników może otworzyć nowe możliwości dla przemysłu chemicznego i farmaceutycznego. Również rozwój materiałów kompozytowych i nanotechnologii przyczyni się do poprawy wydajności urządzeń wykorzystywanych w procesach destylacyjnych. W kontekście ochrony środowiska coraz większy nacisk kładzie się na opracowywanie procesów o niskim zużyciu energii oraz minimalizacji odpadów; technologie takie jak recykling cieczy czy odzysk ciepła będą miały kluczowe znaczenie dla przyszłości przemysłu chemicznego.
Jakie są najważniejsze aspekty bezpieczeństwa podczas destylacji rozpuszczalników
Bezpieczeństwo podczas destylacji rozpuszczalników jest kluczowym zagadnieniem, które należy wziąć pod uwagę w każdym laboratorium i zakładzie przemysłowym. Przede wszystkim, operatorzy powinni być odpowiednio przeszkoleni w zakresie obsługi sprzętu oraz znajomości procedur awaryjnych. Ważne jest również stosowanie odpowiednich środków ochrony osobistej, takich jak rękawice, gogle ochronne oraz odzież robocza, aby zminimalizować ryzyko kontaktu z niebezpiecznymi substancjami chemicznymi. Kolejnym istotnym aspektem jest zapewnienie odpowiedniej wentylacji w pomieszczeniach, gdzie przeprowadzane są procesy destylacyjne, aby uniknąć akumulacji oparów, które mogą być toksyczne lub łatwopalne. Należy także regularnie kontrolować stan techniczny urządzeń oraz instalacji, aby zapobiec ewentualnym wyciekom czy awariom. W przypadku pracy z substancjami łatwopalnymi szczególnie ważne jest przestrzeganie zasad przeciwpożarowych oraz posiadanie odpowiednich gaśnic i systemów alarmowych.